What is the HART protocol?
HART is an open communication protocol commonly used in industrial control systems for remote configuration and data monitoring. Its name comes from the acronym Highway Addressable Remote Transducer.
HART is the global standard for sending and receiving information through the 4-20 mA analog current loops implemented in most field instruments. This technology allows both configuration and parameter data as well as process measurements to be communicated through the 4-20 mA current loop. The instrument control information is digitally modulated over the current loop and therefore there is no interference between them (FieldComm Group, n.d.).
PACTWare
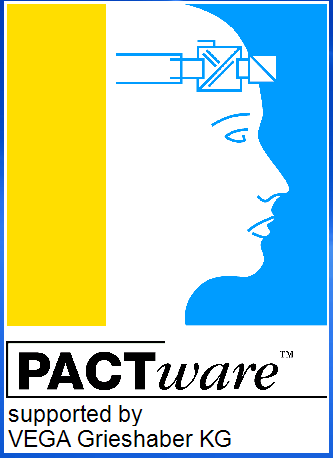
PACTware is a free software application designed to be used independently of manufacturer and fieldbus for easy operation of automation devices. It can be used interchangeably to configure, operate and diagnose all devices in a plant. The software is available free of charge to the user and is the most widely used FDT (Field Device Tool) framework application.
Founded in 2001, the PACTware Consortium e.V. coordinates new and future developments for PACTware software. The association coordinates companies with a variety of sets and skills. The cooperation between suppliers results in a high level of quality and contributes to the broad acceptance of the software by users. The PACTware Consortium e.V. ensures that PACTWare software is continuously developed and is open to new standards.
PACTWare uses a uniform operating and interface concept for all field devices. This means that the user has a simple and recognizable tool for configuring a wide range of field components, depending on the manufacturer. This minimizes the amount of work involved, ensures application safety and reduces training requirements.
Using PACTWare
To use this software tool you will need to download it. From the official PACTWare website, there are several download links depending on the brand of the devices to be configured. In this case, we will use devices from the Vega company (Vega, n.d.).
This company was chosen because the use case in which this tool was used was for the recalibration and data acquisition of level sensors in solids inside metal silos. Therefore, the network structure, datalogger and sensors were already created previously, probably with this tool, although no information is available.
After downloading and installing PACTWare and the Vega plug-ins, we will open the program from the shortcut automatically generated on the desktop: PactWare 5.0.
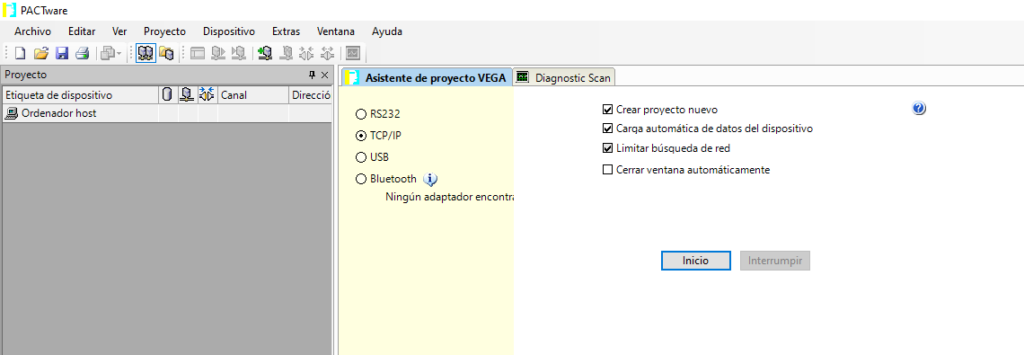
In the start window, we will create a new project and leave the “Automatically load device data” and “Limit network search” options checked. If the PC we are working from is on the same network as the Vega datalogger, PACTWare will be able to detect it and identify the network on which the other sensors are located.
In this example, there is a HART network in which seven sensors are arranged in seven different silos, all connected in series together with the datalogger:
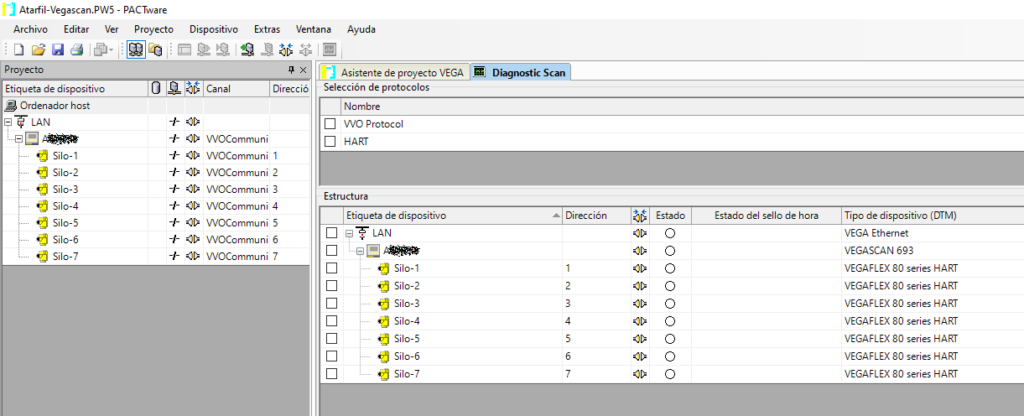
Now you have to establish communication with the devices in the LAN, including the LAN itself. To do this, there are two options: right click on each device and choose “Establish communication” or double click on the icon marked in the following screenshot:
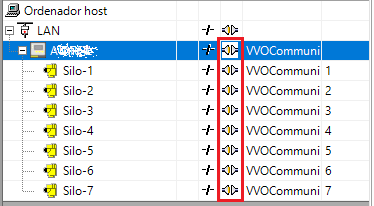
Once the communication is established, to edit online the parameters of each device you will have to right click on the device of your choice and choose the option “Online Parameterization”. Let’s choose the Silo 1 sensor, for example:
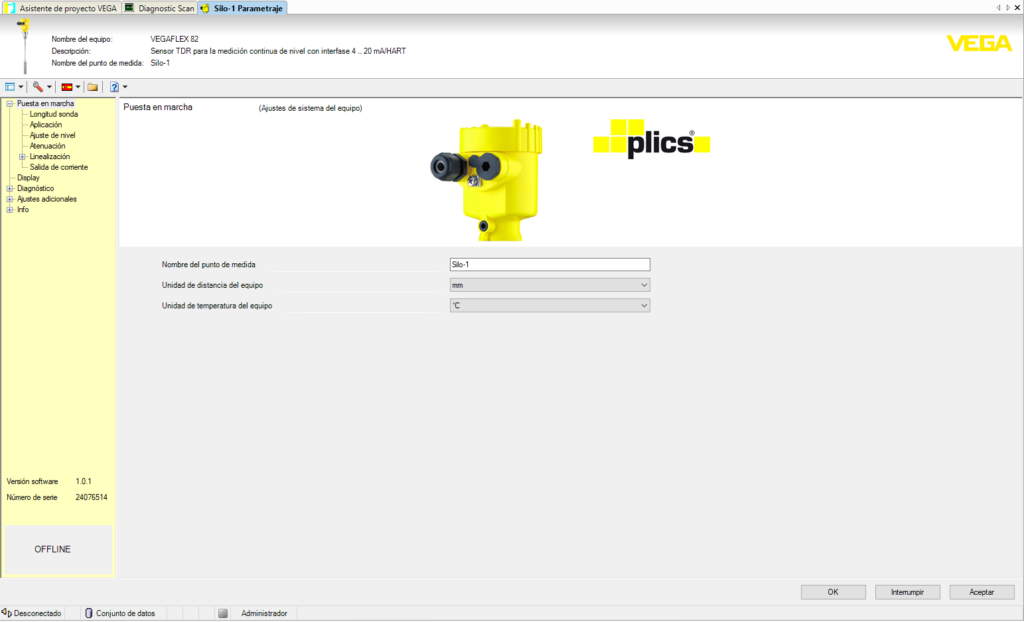
In this example, the parameterization is done offline, since the devices are on a different network than the PC from which I am writing this blog, but the windows and configuration fields are the same.
In this first window, Startup, you can configure the device name, the unit of measurement distance and the unit of temperature of the device.
In the Probe length window, as the name suggests, the length of the probe can be determined either manually or automatically, although for the latter option the silo must be completely empty and there must be no material in contact with the rod.
In “Application”, you can configure the use of this sensor: whether it is for bulk solids or liquids, the type of silo and the product stored in the silo.
In “Level adjustment” you can adjust the distance at which the silo is at 100% and 0% of its capacity.
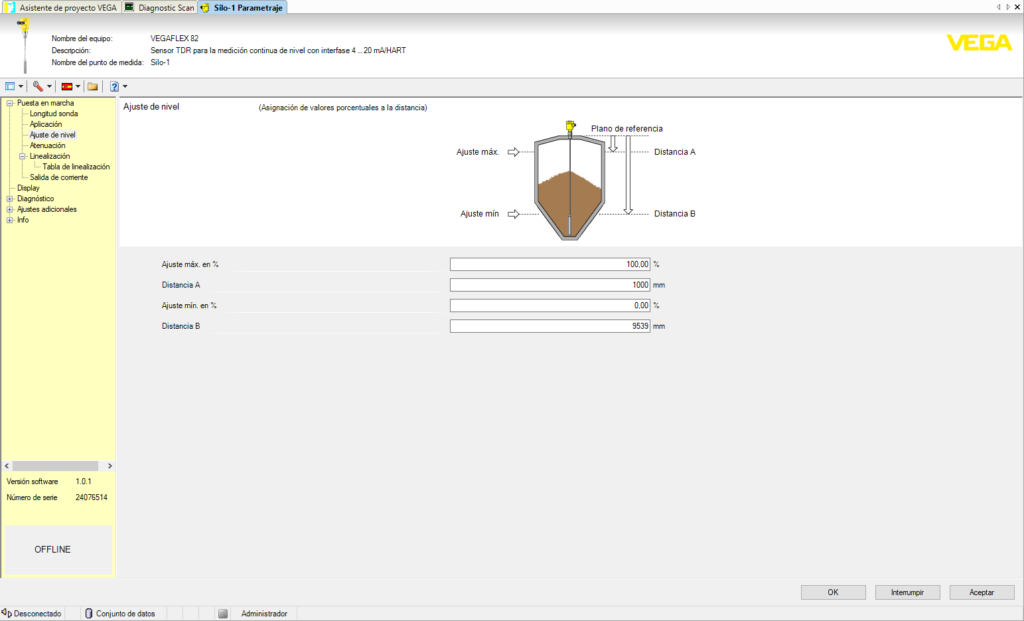
In “Linearization” the linearization of silos having shapes other than perfect cylinders is allowed. For the linearization of these containers, the linearization wizard can be opened to enter a table relating filling height (mm) and occupied volume (m^3).
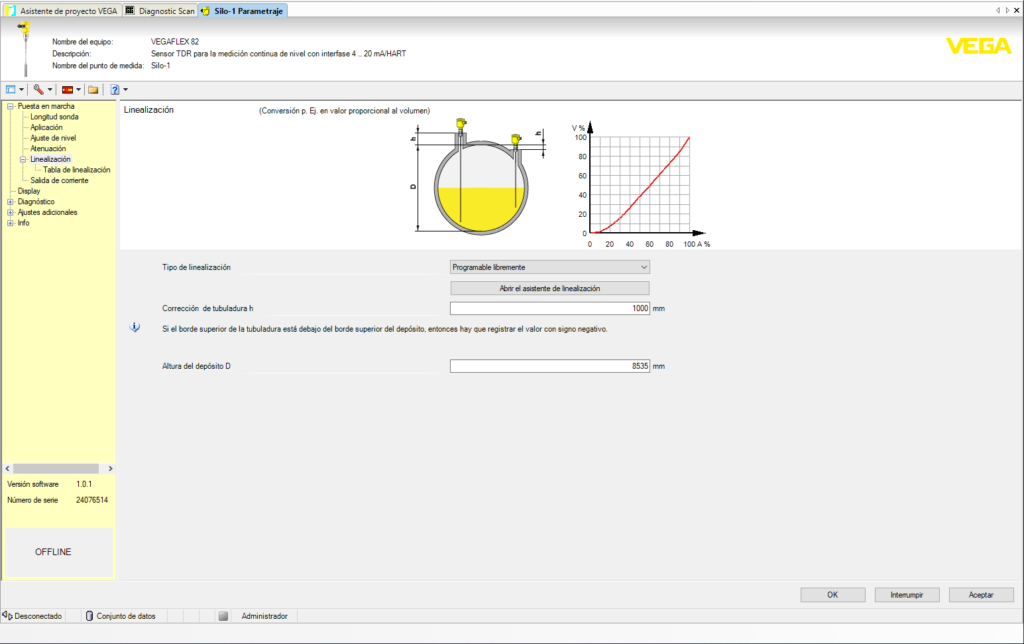
Under “Additional settings”, in “Level scale”, you can choose to which scale value the measured units are converted. In this case, it is a transformation to Volume, in m^3.
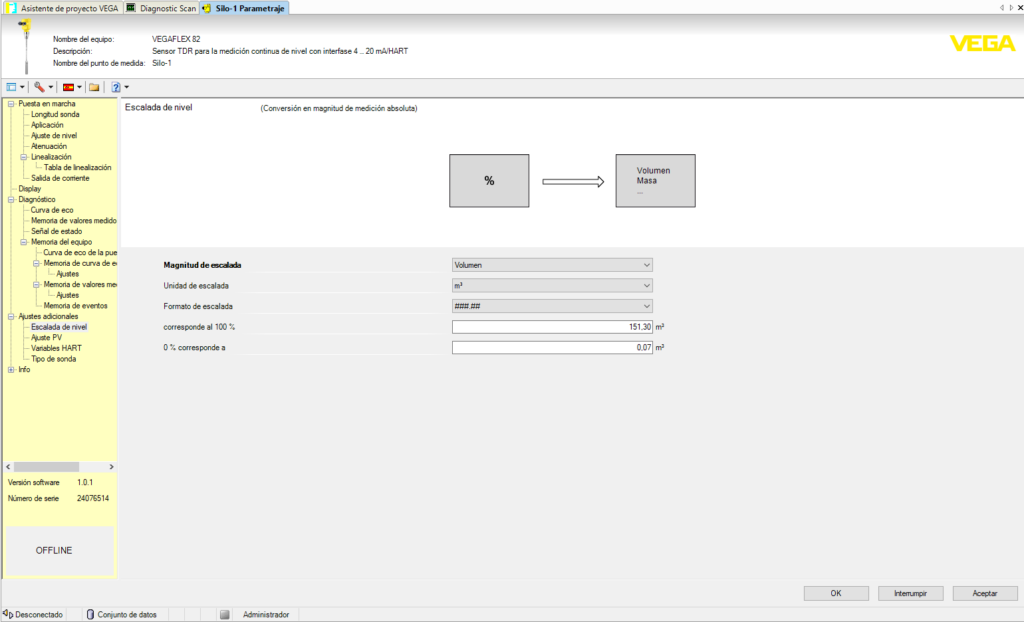
Finally, there are two other windows to configure the variables to be transmitted through the HART protocol: four variables identified as PV (Primary Value), SV (Secondary Value), TV (Tertiary Value) and QV (Quaternary Value). All these variables of each device are transmitted through this protocol. In the “PV Setting” window, the PV to be sent from the device in configuration can be configured, while in “HART Variables” the rest of the variables can be configured.
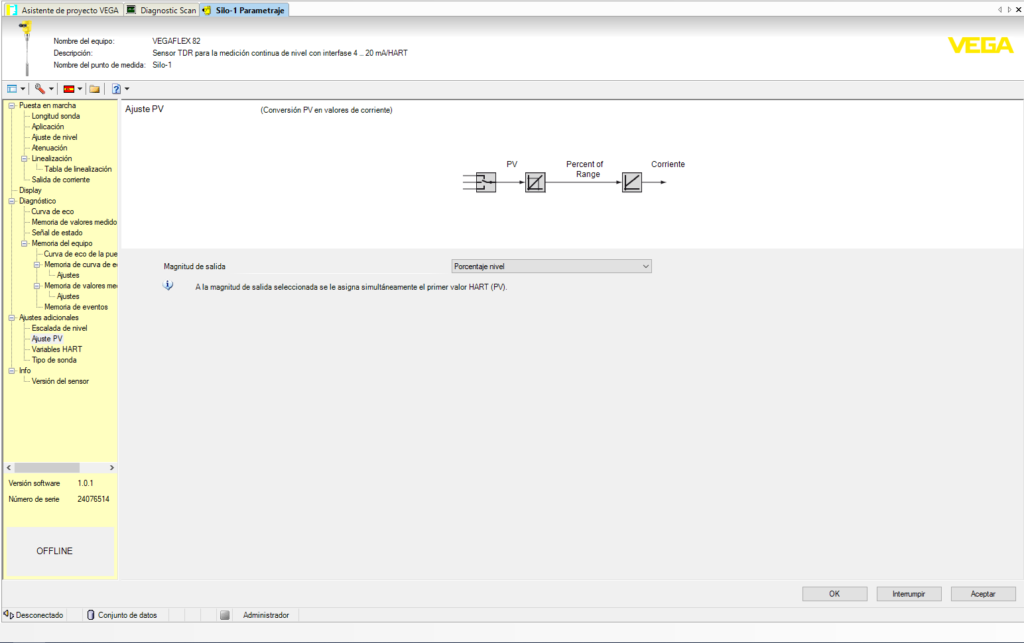
Referencias
FieldComm Group. (s.f.). HART – Digital Transformation For Analog Instruments. Retrieved from https://www.fieldcommgroup.org/technologies/hart
PACTware. (s.f.). Welcome to PACTWare. Retrieved from https://pactware.com/
Vega. (s.f.). Colección DTM y PACTware. Retrieved from https://www.vega.com/es-es/productos/catalogo-de-productos/acondicionadores-de-senal/software/coleccion-dtm-y-pactwar
You really make it appear really easy with your presentation but I find this topic to be actually one thing that I believe I might by no means understand. It seems too complicated and extremely broad for me. I’m looking forward to your next put up, I will try to get the cling of it!